Posts
Showing posts from March, 2010
Posted by
Derek Olson (Oldwolf)
Day Trip to Madison . . . an Awesome Experience
- Get link
- Other Apps
Posted by
Derek Olson (Oldwolf)
Scooby Snacks Keep the Shop Moving Along
- Get link
- Other Apps
Posted by
Derek Olson (Oldwolf)
1500 Baby!!
- Get link
- Other Apps
Posted by
Derek Olson (Oldwolf)
Pros and Cons of a Day in the Shop
- Get link
- Other Apps
Posted by
Derek Olson (Oldwolf)
Friction Tape and the Infinite Search for a Better Way
- Get link
- Other Apps
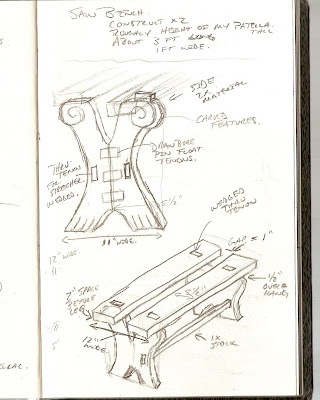
Posted by
Derek Olson (Oldwolf)
More Methods of Work
- Get link
- Other Apps
Posted by
Derek Olson (Oldwolf)
Broken Hearts and Future Changes
- Get link
- Other Apps
Posted by
Derek Olson (Oldwolf)
Will Rehab Help???
- Get link
- Other Apps
Posted by
Derek Olson (Oldwolf)
After the avalanche starts . . .
- Get link
- Other Apps
Posted by
Derek Olson (Oldwolf)
"When you get to the end of your rope. . .
- Get link
- Other Apps
Posted by
Derek Olson (Oldwolf)
Success Can Be So Sweet
- Get link
- Other Apps